Unlocking Efficiency: The Role of OEM Wire and Cable Equipment in Modern Manufacturing
Release time:
2025-04-25
Unlocking Efficiency: The Role of OEM Wire and Cable Equipment in Modern Manufacturing Manufacturing is an ever-evolving field, and the demand for efficiency, quality, and innovation keeps growing. **Original Equipment Manufacturer (OEM)** wire and cable equipment plays a pivotal role in modern manufacturing, particularly in sectors that focus on electronics and electrical products. The integratio
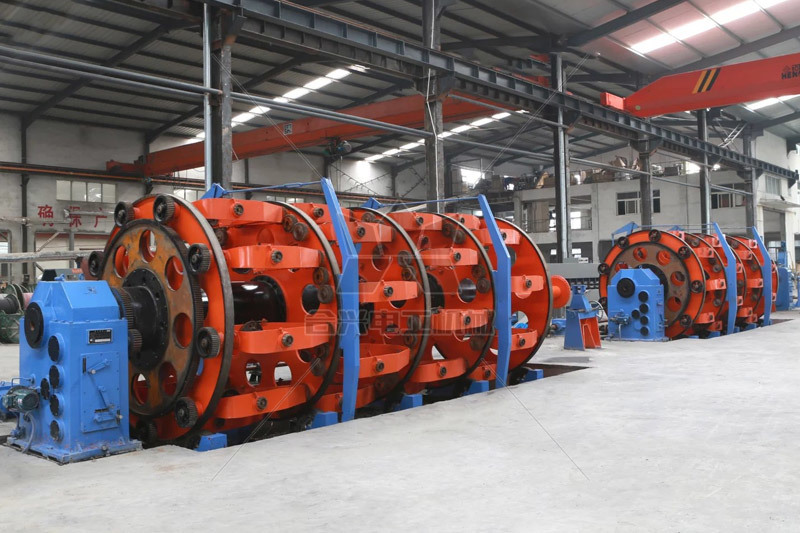
Unlocking Efficiency: The Role of OEM Wire and Cable Equipment in Modern Manufacturing
Manufacturing is an ever-evolving field, and the demand for efficiency, quality, and innovation keeps growing. **Original Equipment Manufacturer (OEM)** wire and cable equipment plays a pivotal role in modern manufacturing, particularly in sectors that focus on electronics and electrical products. The integration of advanced OEM equipment not only streamlines production processes but also enhances product quality and overall operational efficiency. In this article, we will explore the vital role of OEM wire and cable equipment in modern manufacturing, focusing on their benefits, technological advancements, and implementation strategies.
Table of Contents
1. Introduction to OEM Wire and Cable Equipment
2. Benefits of Using OEM Wire and Cable Equipment
- 2.1 Quality Assurance and Compliance
- 2.2 Cost Efficiency in Manufacturing
- 2.3 Reduced Downtime and Enhanced Productivity
3. Technological Advancements in OEM Equipment
- 3.1 Automation in Wire and Cable Manufacturing
- 3.2 Integration of Smart Technology
4. Implementing OEM Wire and Cable Equipment in Your Facility
- 4.1 Evaluating Your Manufacturing Needs
- 4.2 Choosing the Right OEM Partners
5. Case Studies: Success Stories in OEM Implementation
6. Future Trends in OEM Wire and Cable Equipment
7. FAQs
8. Conclusion
Introduction to OEM Wire and Cable Equipment
In the manufacturing landscape, **OEM wire and cable equipment** refers to specialized machinery designed to produce high-quality wires and cables tailored for various applications. These machines can range from simple wire drawing machines to complex multi-functional cable manufacturing lines. OEMs focus on producing equipment that meets the specific requirements of manufacturers, ensuring compatibility, durability, and performance. As a result, businesses leveraging OEM equipment can streamline their production processes, enhance product quality, and reduce costs.
Benefits of Using OEM Wire and Cable Equipment
Incorporating OEM wire and cable equipment into manufacturing processes offers numerous advantages. Below, we discuss some of the key benefits that make OEM solutions indispensable in modern manufacturing.
Quality Assurance and Compliance
**Quality assurance** is crucial in manufacturing, especially in industries such as electronics and automotive, where safety and performance are paramount. OEM wire and cable equipment is designed to adhere to strict industry standards and regulations, ensuring that products meet or exceed quality expectations. By using OEM equipment, manufacturers can achieve consistency in production, resulting in fewer defects and higher customer satisfaction.
Cost Efficiency in Manufacturing
Cost control is a top priority for manufacturers aiming to maximize profits. OEM wire and cable equipment enables organizations to achieve **cost efficiency** through optimized production processes. These machines often incorporate energy-efficient technologies that reduce operational costs. Additionally, by minimizing waste and improving yield, manufacturers can significantly lower their material costs, contributing to overall financial health.
Reduced Downtime and Enhanced Productivity
**Downtime** can severely impact manufacturing efficiency and profitability. OEM equipment is engineered for reliability, minimizing the risk of breakdowns and interruptions during production. Advanced features such as predictive maintenance and real-time monitoring allow manufacturers to identify potential issues before they lead to failure. Consequently, businesses can maintain smooth operations, enhance productivity, and meet customer demands promptly.
Technological Advancements in OEM Equipment
As technology continues to evolve, OEM wire and cable equipment is becoming increasingly sophisticated. Innovations in machinery design and functionality are reshaping manufacturing practices and opening new possibilities for efficiency.
Automation in Wire and Cable Manufacturing
**Automation** is a game-changer in manufacturing, and OEM wire and cable equipment is at the forefront of this revolution. Automated systems can handle repetitive tasks with precision, reducing the need for manual labor and minimizing human error. This shift not only enhances production speed but also allows workers to focus on more strategic tasks, further increasing overall operational efficiency.
Integration of Smart Technology
The rise of **smart technology** in manufacturing has led to the development of intelligent OEM equipment that can communicate with other machines and systems. This connectivity enables manufacturers to gather valuable data on production performance, monitor equipment health, and optimize resource utilization. By leveraging smart technology, organizations can make data-driven decisions that enhance efficiency and drive continuous improvement.
Implementing OEM Wire and Cable Equipment in Your Facility
Transitioning to OEM wire and cable equipment requires careful planning and execution. Here, we outline essential steps for successful implementation.
Evaluating Your Manufacturing Needs
Before investing in OEM equipment, it is crucial to conduct a thorough assessment of your manufacturing needs. This evaluation should include an analysis of current production processes, capacity requirements, and quality standards. Understanding your unique needs will help you choose the right OEM solutions that align with your business objectives.
Choosing the Right OEM Partners
Selecting the right OEM partners is essential for a successful implementation. Look for manufacturers with proven expertise in wire and cable equipment and a track record of delivering reliable, high-quality solutions. Engage with potential partners to discuss your requirements and evaluate their ability to meet your specifications. Strong partnerships can lead to better support, maintenance, and long-term success.
Case Studies: Success Stories in OEM Implementation
Examining real-world examples of successful OEM equipment implementation can provide valuable insights for manufacturers. Here, we highlight a few case studies that demonstrate the impact of OEM wire and cable equipment on operational efficiency.
**Case Study 1: Automotive Wiring Solutions**
An automotive manufacturer faced challenges with production delays and high defect rates in their wiring harnesses. By integrating OEM wire drawing and assembly equipment, they achieved a 30% reduction in production time and improved product quality, resulting in increased customer satisfaction.
**Case Study 2: Telecommunications Cables**
A telecommunications company struggled with outdated equipment that led to frequent breakdowns and increased maintenance costs. They invested in state-of-the-art OEM cable manufacturing lines, which boosted productivity by 40% and reduced downtime significantly. The transition enabled them to meet growing market demands without compromising quality.
Future Trends in OEM Wire and Cable Equipment
As we look to the future, several trends are likely to shape the landscape of OEM wire and cable equipment.
**Sustainability** will become a dominant focus, with manufacturers seeking eco-friendly solutions that minimize waste and energy consumption. The adoption of **Industry 4.0** principles will continue to rise, pushing for greater automation and smart manufacturing practices. Additionally, advancements in **materials science** may lead to the development of more efficient and durable wire and cable products, further enhancing performance.
FAQs
**1. What is OEM wire and cable equipment?**
OEM wire and cable equipment refers to specialized machinery designed for the production of wires and cables, tailored to meet industry standards and manufacturer specifications.
**2. What are the benefits of using OEM equipment?**
Benefits include improved quality assurance, cost efficiency, reduced downtime, and enhanced productivity in manufacturing processes.
**3. How does automation impact OEM wire and cable manufacturing?**
Automation allows for precision, speed, and reduced manual labor, leading to increased efficiency and minimized human error throughout the production process.
**4. What should I consider when choosing an OEM partner?**
Evaluate the partner's expertise, track record, ability to meet your specific needs, and the quality of their support and maintenance services.
**5. What are the future trends in OEM wire and cable equipment?**
Key trends include a focus on sustainability, the rise of Industry 4.0 practices, and advancements in materials science for enhanced product performance.
Conclusion
In conclusion, OEM wire and cable equipment is integral to achieving efficiency and quality in modern manufacturing processes. By selecting the right OEM solutions and implementing them effectively, manufacturers can optimize their operations, reduce costs, and enhance product quality. As the industry continues to evolve with advancements in technology and a focus on sustainability, those who embrace OEM equipment will be well-positioned to thrive in a competitive market. The path to unlocking efficiency lies in the strategic integration of these innovative solutions into manufacturing processes.
TAG:
Recommend News
HEXING CABLE MACHINERY
TEL: +86-317-3601666, +86-317-3236119
FAX: +86-317-3618408
E-MAIL: china@hbhxdg.cn
E-MAIL: hbhxdg@gmail.com
WEB: http://www.hbhxdg.cn
ADD: Baoantun Industrial Zone, Hejian City, Hebei Province